Projects
Each project we undertake reflects our commitment to precision, performance, and progress. From complex utility installations to innovative trenchless solutions, ECI Contracting delivers reliable results through skilled union labor and proven expertise in the field.
ECI Project Profile
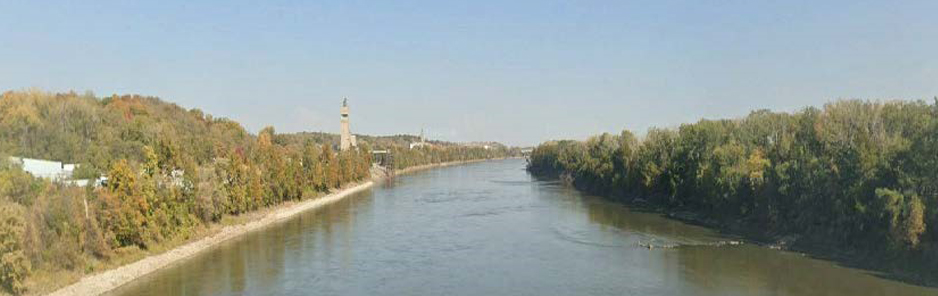
Buckeye Creek Crossing
City of Kansas City, MO – 3,825 LF of 36-inch HDPE Intersect
Project Details
- 3,825 LF
- $2.5MM
- Intersect Install
- Gyroscopic Steering
Buckeye Creek Force Main
City of Kansas City
Spring of 2021, ECI Contracting partnered up on a project crossing the Buckeye Creek in Kansas City, MO. ECI was tasked with the installation of 3,825 feet of 36-inch HDPE for a new force main for the city of Kansas City. Due to large diameter and length, ECI utilized the intersect method of installation.
ECI Scope
ECI partnered with a construction firm to install the new Forcemain for the City. With the complexity of the install, ECI chose a few methods to increase project success.
Technical Solution
Working with the General Contractor, we did a project risk review. Noting the formational changes between the soils, shale and limestone bedrocks, ECI Contracting acknowledged we needed to make the following decisions:
- Utilized gyroscopic steering system for increase accuracy in layered rock formations
- Deployed two crews for intersect installation
- Implemented specialized drilling mud program for transitioning geologies.
- 54-inch Casing installation to support circulation during HDD Operations
- Hired security to ensure safety of the public due to in-town project
Project Execution
Once Mobilized, ECI Contracting pushed forward on the project plan. Gyroscopic steering was a critical use item for the installation over large body of waters. Utilizing the accuracy during the installation improves the time to intersect, which has added importance in rock situations.
The 54-in conductor casing was installed due to fractured formations at the beginning of the HDD. Transitioning from jettable soils to rock can be challenging, adding fractured rock and cobbles creates a more complex challenge. After installing the 54-in conductor casing, ECI utilized 16-in centralizer casing for the pilot process of the HDD.
The Intersect installation method was chose to increase the torque of the drilling tool against the rock formation. ECI recognized this as a benefit due to the layered limestone, which can cause difficulties facing the tool against the geology. Bringing in a secondary machine with additional mud system allows additional pulling capability to maximize cutting time, and tool life production. Allowing circulation of soil cuttings to both the entry and exit pit locations allows for more efficient mud cleaning and minimizing project down time.
Result
The project was completed in approximately three months. After a successful intersect, the ECI team finished the excavation with 24, 36, and 48-inch diameter ream passes. Preparing for extended pullback operations, ECI started in the morning and continued pulling until the pipe was installed.
Relevance
Large diameter HDPE can come with its own challenges. Working with an HDD contractor with experience is a crucial part of any project. ECI Contracting brings the experience to the project to ensure a successful project. With over 100 Large Diameter HDPE installations, ECI brings turn-key convenience and peace of mind.
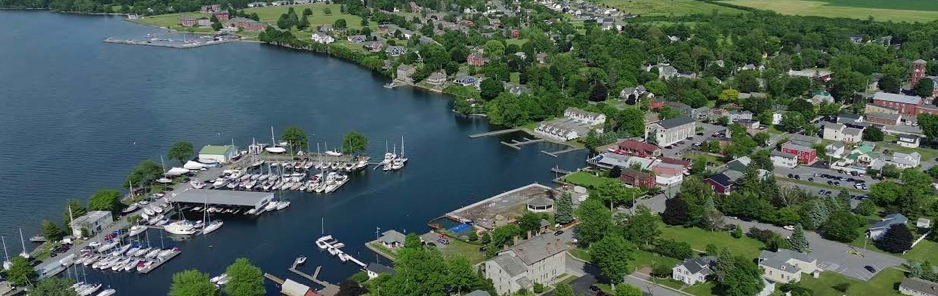
City of Sackets Harbor, NY
1200’ of 20” HDPE – Outfall into Lake Ontario
Project Details
- 1,200 LF
- 20-inch HDPE
- $1.1 MM
As a leader in Horizontal Directional Drilling (HDD), ECI Contracting was subcontracted to provide specialized services as part of a larger project to install 1,200 linear feet of 20-in diameter HDPE pipe waterward from the shoreline of Lake Ontario at the Village of Sackets Harbor, New York Water Treatment Plant. The completion of this project hinged on the successful completion of horizontal directional drilling to meet underwater pipe that would be installed via the float and sink method from the lake surface using barges.
ECI Scope
While ECI Contracting is no stranger to horizontal directional drilling, this particular project presented some unique challenges, including:
- Shallow drilling depth (15 to 20 feet) in Limestone rock
- Complex operations in active waterway
- Offshore work utilizing barges on the lake surface that required creative
- solutioning and specialized equipment
Technical Solution
After careful consideration and on-the-ground assessment, our team of experts created and implemented a sophisticated drilling and installation approach based on customer tolerances and specifications:
- Deployed a Prime 250 Maxi Directional Drill Rig
- Utilized conventional wireline steering system with offset coil configuration
- Implemented specialized drilling mud management for rock penetration
- Coordinated a multi-phase installation process:
-
- Drilling a shore-based pilot hole
- Offshore reaming operations
- Pipe flotation and pull-back procedures
Project Execution
Working in collaboration with the general contractor, the successful completion of this project required precise coordination between multiple operations, including:
- Shore-based drilling operations
- Offshore barge-supported excavation
- Pipe fusion and assembly
- Underwater pull-back operations
- Integration with existing infrastructure
Results
Over the course of four weeks, our team successfully managed the installation of 1,200 LF of 20-inch HDPE from the shoreline into Lake Ontario. The installation was completed at a maximum depth of 40 feet, utilizing excavators on offshore barges to support post-pilot operations. All together successfully installing the new water intake pipe for the city of Sackets Harbor, NY.
Highlights
- Collaboration with the general contractor and municipal authorities ensured delivery of the upgrade on schedule and within budget
- Through careful observation and experience, our team adapted to the challenges presented and executed creative and technical solutions to achieve success
- Maintained drilling accuracy in spite of challenging conditions to achieve seamless integration with the existing infrastructure
- Completed the installation with minimal environmental impact, reducing disruption to the natural surroundings
Relevancy
Offshore drilling operations can always be a challenge. Working before the project starts, pre-construction planning is critical to have success in the field. Creating a project plan with an experienced team takes the pressure off, and ECI has the team to do it. With multiple Superintendents and drillers with offshore experience, we know how to handle the small details.
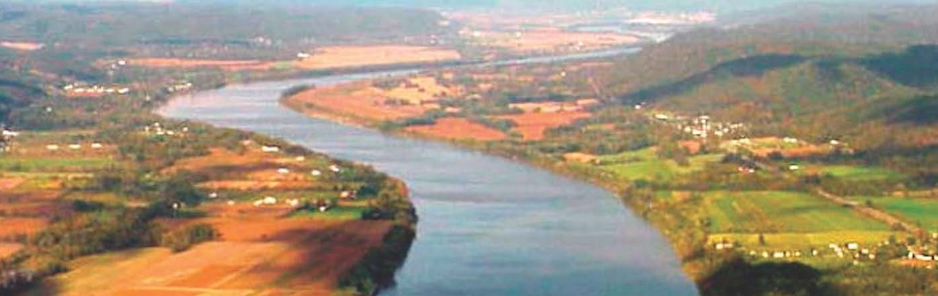
Shell Falcon
54,150’ of 12” and 16” steel with 1 7200’ 12” intersect Ohio River Crossing
Project Details
- 54,150 LF of 12 & 16-inch steel
- $35MM
- Six crews running for 18 months of maxi-drill rig installations
- Multiple Gyroscopic steering including a horizontal curve intersect installation
In 2018, ECI Contracting was subcontracted to provide Horizontal Directional Drill installation services for the Shell Falcon Ethane Pipeline System in Ohio/Pennsylvania/West Virginia. The project included 97.5 miles of total pipe installation, with 25 HDD’s of varying lengths. The completion of this project was required to connect multiple processing facilities across critical resources including the Ohio River.
ECI Scope
Working a multi-stage, multi-bore project can be a challenge to manage. This particular project presented some unique challenges on top of large scale logistics, including:
- Multi-layered geology of soft-hard rock
- Sandstone
- Limestone
- Claystone
- Siltstone
- Coal seams including large voids
- Extreme elevation changes
- High population and heavily trafficked areas
Technical Solution
After evaluating the risk areas of the project, our team of experts created and implemented unique drill plans for each location that took into the specific challenges of each HDD:
- Deployed six total crews including Midi (200k lb.) to Maxi (660k lb.) directional drill rigs
- Utilized conventional wireline steering system as well as gyroscopic steering as needed
- Implemented specialized drilling mud program for rock penetration and void plugging management.
- Casing installation to support circulation during HDD Operations
- Installed Sound Mitigation on select locations to minimize noise impact
Project Execution
Working in collaboration with the general contractor, ECI managed to complete the project on schedule, maximizing crew efficiencies.
- Ohio River intersect
- Over 100’ elevation changes
- Compound curve steering
- Electronic Data Reading for automated data collection
- Multi-Tier jobsites due to limited work space on hill sides
- Managed a multitude of teamsters for logistical movement of equipment, refuse, and soils disposal to maintain clean, safe work sites.
Result
Over the course of two years, our team successfully managed the horizontal directional drilling operations and logistics of six crews. Utilizing both wireline magnetics, and gyroscopic steering, ECI was able to successfully install to tolerance in a multitude of geologies.
Highlights
- Collaboration with multiple municipalities, Unions, and project teams.
- 7,200 foot installation across the Ohio River with an intersect utilizing gyroscopic steering.
- Examined and created mitigation plans for difficult geology including circulation challenges in coal seams.
- Utilization of Electronic Recording Devices – Pushing new technology for more efficient and accurate project data.
Relevance
ECI Contracting is a reliable firm that promises Integrity, Teamwork, Grit, Accountability, and Family Values on all projects. When the challenges seem astronomical, ECI Contracting digs deep to create a product that adds value in addition to fulfilling a customer’s needs.